A Beginner’s Guide To Understanding Diesel Engines
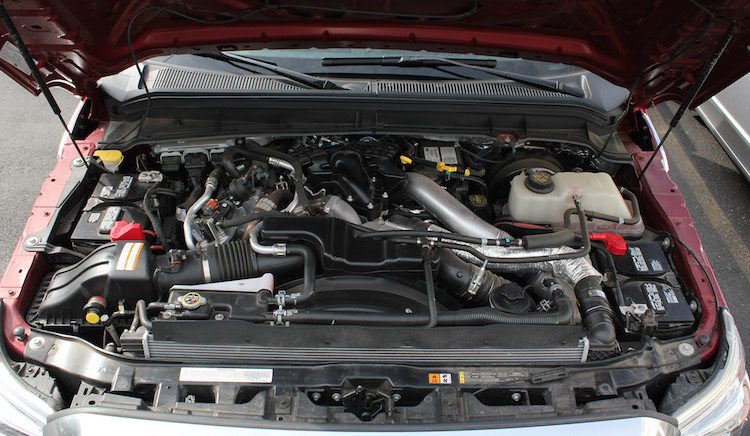
By Mike McGlothlin
It’s no secret that the majority of Americans are more accustomed to gasoline engines than diesels. Statistics gathered by R.L. Polk confirm this, as just 2.8 percent of all registered passenger vehicles (cars, SUV’s, pickup trucks, and vans) ran on number 2 diesel fuel in 2013. To be sure, most folks in the U.S. expect to find spark plugs or coil packs when they pop the hood, not turbochargers and injection pumps (two very key elements on nearly every diesel engine you’ll come across, hence the term “turbodiesel”).
In order to gain an understanding of the differences between diesel and gasoline engines, we’ll begin with all of the similarities shared between the two. The type of fuel burned by either power plant doesn’t change anything in relation to the engine’s general makeup (i.e. a crankshaft spinning, connecting rods and pistons moving up and down, air being pumped in, and exhaust being routed out). In fact, the same basic architecture is very much the same. But what goes on in-cylinder in a diesel is vastly different from what you’ll find in its gas-powered counterparts.
The easiest way to explain the difference between gasoline and diesel engines is with “air” and “fuel.” In a gasoline engine, airflow is everything. You’re throttling air. A diesel mill is the polar opposite. It works on the premise of throttling the amount of fuel being injected—the air simply follows suit. Therefore there is no need to throttle the incoming air. To that end, there is also no vacuum created within a diesel engine.
Intake Air
For our purposes, we’ll use a four-stroke, turbocharged and intercooled diesel engine to illustrate the flow of air and fuel throughout a modern diesel power plant. Fresh air enters the compressor housing (intake side) of the turbocharger and is compressed in the compressor wheel, where boost is created. This makes the air denser, but also much warmer.
To cool off the compressed air before it enters the cylinder head(s), it is routed through a charge air cooler (also known as an intercooler). The most frequently used intercooler type is of an air-to-air style, and is essentially just a simple heat exchanger. The intercooler significantly lowers the temperature of the intake air along its journey to the engine, and does so with a very minimal loss in boost.
Compression Ignition
Things get interesting once the compressed air is forced in-cylinder. During the intake stroke—where the piston is dropping to the bottom of its range—the intake valve(s) opens, allowing “unthrottled” air to fill the cylinder. This is different from a gasoline engine in two ways: 1) gas engines introduce a mixture of fuel and air during the intake stroke, and 2) in a diesel, air is only drawn in during the intake stroke. Next, the intake valve(s) closes and the compression stroke begins. As the piston travels upward, the air that once filled the cylinder now consumes just 6% of the area it did before. This air, under tremendous pressure, instantly becomes super-heated to more than 400 degrees—which is more than enough heat to make diesel fuel ignite on its own. And, at the top of the piston’s stroke that’s exactly what happens. The previously mentioned super heated air is met with a shot of diesel fuel (released into the cylinder by its respective fuel injector) during the perfect window of time before the piston reaches top dead center, and combustion occurs. Because a diesel engine uses the heat of compression to ignite its fuel, no aid to begin the combustion process is needed (i.e. spark plugs, such as in a gasoline engine).
Turbochargers Make Diesels What They Are: Great
The last order of business is the exhaust stroke, where spent combustion gasses are forced out of the exhaust valves, through the exhaust manifold, and into the turbine (exhaust) side of the turbocharger. In your average gasoline-powered engine no turbocharger exists, which means once out of the engine, exhaust gasses immediately head for the tailpipe. This is not so in a diesel, as the turbocharger, which is in charge of forcing fresh air into the engine, actually uses the exhaust gasses leaving it to drive itself. Because a turbocharger consists of a turbine (exhaust) wheel sharing a common shaft with a compressor (intake) wheel, exhaust gasses are always required in order to bring air into the engine. One depends on the other. We’ll break down the importance of the turbocharger like this: You throttle fuel (sending diesel into the engine), combustion occurs, exhaust gasses leave the engine, spinning the turbine wheel on the way out, which turns the compressor wheel, introducing air into the engine. An endless cycle, if you will. The thermal efficiency of the diesel engine is improved by the turbocharger, as it increases the volume of air entering it, which lays the groundwork for combustion of more fuel.
Differences In Combustion
One of the primary differences between diesel and gas engines exists in the type of combustion each uses. As was discussed above, in a diesel, when fuel finally meets the compressed in-cylinder air, combustion is the result. In a gasoline engine, fuel and air mix before combustion ever takes place. But on top of that, each engine’s combustion chamber has a different location. In a typical gasoline engine, the combustion chamber is recessed into the cylinder head(s). In a direct injection diesel engine, the combustion chamber is actually inside the piston. This combustion chamber is most commonly of the “Mexican Hat” design, which consists of a recessed hole in the center of the piston. At the bottom of this recession, a cone-shaped protrusion exists. With the fuel injector positioned directly above it, it is this protrusion that allows optimized fuel atomization and the perfect combustion process to take place. More than 99 percent of all diesel engines utilize the Mexican Hat design due to the center of the piston receiving the brunt of the combustion explosion, not the piston crown. This gives the piston exceptional reliability.
Direct Injection
In simple terms, direct injection means the system’s injectors protrude and spray directly on top of the piston. There is no pre-chamber or swirl chamber, and fuel doesn’t have to make its way through the intake manifold before entering the cylinder. With direct injection, the entire combustion process is quicker, simpler, and much more efficient than it is in a typical, multi-port fuel injection gasoline engine. Direct injection diesels also operate at very lean air/fuel ratios in comparison to gasoline engines. A typical air/fuel ratio between 25:1 to 40:1 (diesel) vs. 12:1 to 15:1 (gasoline) offers some insight as to why diesels are so conservative on fuel consumption. Efficiency is further illustrated by the fact that modern day direct injection diesel engines inject fuel at pressures approaching (or in some cases, exceeding) 30,000 psi. This provides the finest atomization possible for not only an efficient burn, but also one that is low on waste heat.
Start Of Injection vs. Timing
While the term “timing” is often heard in both the gasoline and diesel world, this one word means two very different things depending on which type of engine you’re dealing with. Needless to say, it’s important to distinguish between the two. In a gasoline engine, timing refers to the start of combustion. In a diesel, timing is the start of injection, or SOI (when the injector begins to spray fuel into the cylinder). Again, it all comes back to fuel (and the injection system) being the key aspect of a diesel engine.
Torque. Lots Of It.
It’s common for someone unfamiliar with diesel engines to question why or how they create the impressive amounts of torque they do. The torque-to-horsepower ratio in diesel engines is rarely lower than 2:1, and it’s typical to see ratios of 3:1 and even 4:1 in heavy-industry engine applications. Gasoline engines are much closer to a 1:1 ratio. The reason why diesel engines produce so much torque stems from three key things: 1) boost created by the turbocharger, 2) stroke, and 3) cylinder pressure.
At the present time, production diesel engines see 25 to 35 psi of boost straight from the factory. By comparison, 10 psi of boost is oftentimes considered excessive when seen in gasoline engines. The best thing about compressed intake air (i.e. boost) in a diesel engine is that it decreases the pumping losses of the engine on the intake stroke, and increases cylinder pressure on the power stroke (combustion).
Long stroke crankshafts have always been conducive to making torque, whether in a gasoline or diesel engine. But why? Look at it as if you’re using a long wrench to loosen an extremely tight bolt, rather than the shorter wrench that couldn’t get the job done to start with. You can apply more torque with more leverage, right? Of course you can. In a long stroke engine, the connecting rod can apply more leverage in turning the crankshaft (while the piston descends during the power stroke): hence more torque.
As you may have already deduced, the type of cylinder pressure that produces torque is created during the power stroke. Lengthening the injection event that occurs in cylinder with an earlier start of injection (SOI) will effectively generate more pressure on top of the piston. With greater pressure being generated on top of the piston, more torque is created.
Overbuilt
Extreme cylinder pressure, long strokes, and high boost levels not only explain why diesels create torque, but they are also why diesel power plants are built with such heavy-duty components. To withstand the tremendous stresses imposed on them, manufacturers use things like deep-skirt cast-iron (and even compacted graphite iron) blocks, forged-steel crankshafts and connecting rods, and typically use cylinder heads with at least 6 head bolts per cylinder. All-steel pistons even get the nod in plenty of heavy industry and Class 8 engine applications. For longevity purposes, diesel engines are overbuilt. In small displacement diesels, it’s not uncommon to find the factory cross-hatching still present in the cylinders after 300,000 miles of use. And it’s par for the course for an over-the-road Class 8 engine to go 750,000 to 1,000,000 miles between overhauls.
Diesel Is Here To Stay
The method of combustion, fuel injection, and ignition employed in a diesel engine definitely sets it apart from its gasoline counterpart. Diesel’s fuel economy advantage over gasoline power plants is something that has brought it to the forefront of today’s fuel economy conversation. With CAFE (corporate average fuel economy) standards quickly approaching, the buzz around hybrid cars seemingly flat lining, and electric vehicles failing to offer adequate range, more manufacturers will turn to diesel power plants in the years ahead than ever before. Rest assured, diesel engines are not only here to stay—they very well may be the engine of the future.
Sources:
Diesel Power Magazine
April, 2009 issue, page 50
The Diesel Forum (R.L. Polk data)
http://www.dieselforum.org/resources/top-10-states-of-diesel-drivers
TTS Power Systems (Start of Injection)
Book: “Modern Diesel Technology: Diesel Engines”
By Sean Bennett
How It Works: Diesel Engines
https://www.motortrend.com/features/1208dp-how-it-works-diesel-engines/